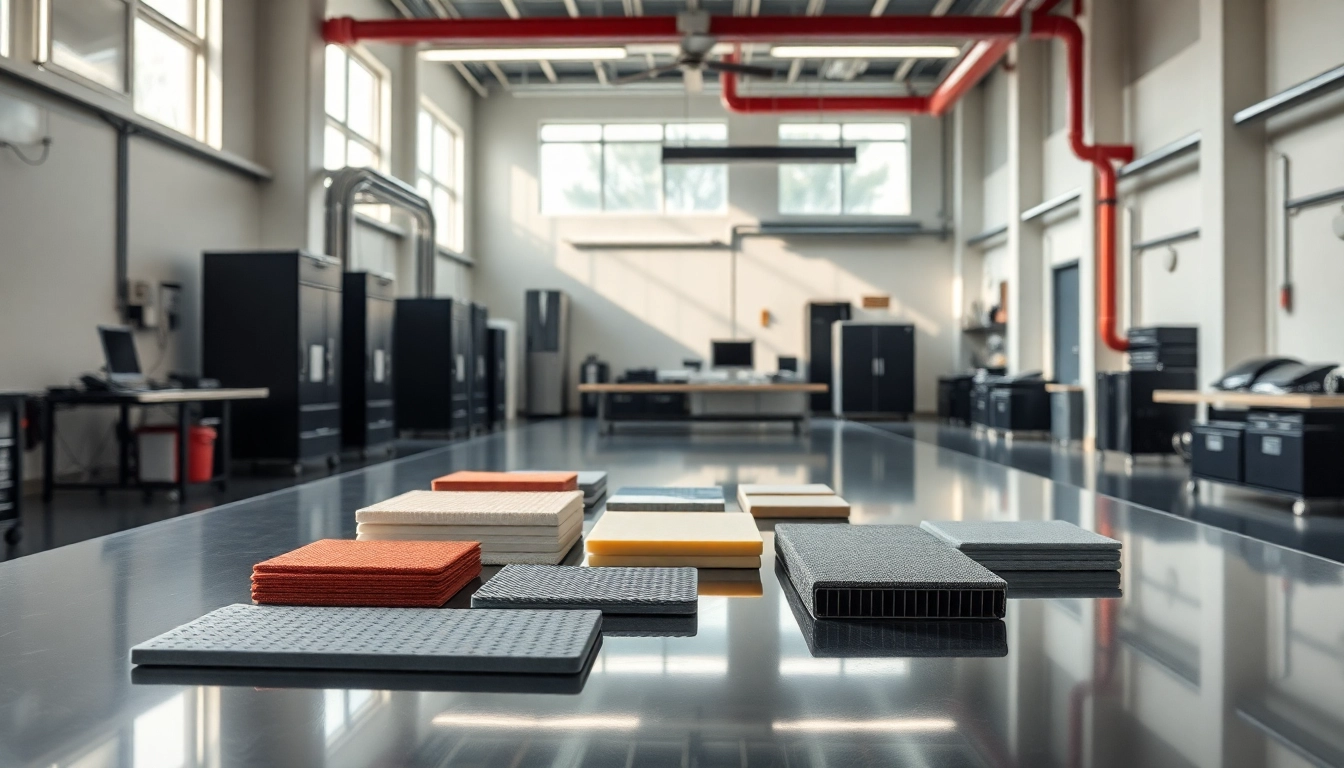
Understanding Thermal Management Materials
Thermal management is a critical aspect in the design and operation of electronic devices, ensuring that excess heat is effectively dissipated. At the core of this process lies thermal management materials, which aid in thermal regulation across various applications. These materials play an essential role in enhancing device performance, longevity, and safety by regulating heat flow in electronics and other sectors. In this article, we will delve into the significance of thermal management materials, their types, key characteristics, applications, selection criteria, and future trends that shape this evolving industry.
What Are Thermal Management Materials?
Thermal management materials encompass a variety of products designed to control and dissipate heat, crucial in numerous technological applications. The primary goal of these materials is to minimize thermal resistance between heat-generating components and heat sinks or other heat-dissipating structures. Common forms of thermal management materials include thermal interface materials (TIMs), gap fillers, thermal pads, thermal greases, and phase change materials (PCMs).
Each category has unique properties and applications suited to varying thermal management needs. For example, thermal interface materials are typically used for improving thermal contact between surfaces, while gap fillers are valuable for filling irregular spaces that act as thermal barriers. The correct application of these materials can significantly reduce the risk of overheating in electronic products, ensuring their reliability and efficient operation.
The Importance of Thermal Management in Electronics
As devices become increasingly compact and powerful, the management of heat has become a pivotal concern. Excessive heat can lead to reduced performance, malfunction, and ultimately, failure of electronic components. Effective thermal management is essential not only for the device’s functionality but also for compliance with safety regulations and enhancing user experience.
Moreover, the reliability of electronics in industries such as automotive, aerospace, and consumer electronics is heavily reliant on proper thermal management strategies. By implementing the right thermal management materials, manufacturers can ensure optimal performance and longevity, thereby protecting their investments and fostering customer satisfaction.
Types of Thermal Management Materials Available
Given the diverse applications and requirements of thermal management, a variety of materials are available. The most common types include:
- Thermal Interface Materials (TIM): These materials improve thermal contact between heat sources and heat sinks. They can be in the form of greases, pads, or phase change materials.
- Gap Fillers: Soft and conformable, gap fillers are used to fill spaces between components and provide thermal conductivity.
- Thermal Pads: Available in various thicknesses and materials, these pads provide thermal conductivity and act as insulators.
- Thermal Tapes: Pressure-sensitive adhesives designed for thermal management applications, often used for securing components and ensuring a thermal bond.
- Phase Change Materials (PCMs): These materials absorb and release thermal energy during phase transitions, maintaining a stable temperature range under varying loads.
Key Characteristics of Effective Thermal Management Materials
Thermal Conductivity Explained
One of the most critical metrics in assessing the performance of thermal management materials is thermal conductivity, measured in watts per meter-Kelvin (W/mK). This property refers to the ability of a material to conduct heat, which is crucial in preventing overheating in electronic devices. High thermal conductivity materials such as metals (copper and aluminum) are often preferred for their effectiveness in heat transfer.
While numeric values are essential, the practical implementation of thermal conductivity also hinges on the interface between materials. Even a material with high conductivity can underperform if the surface areas in contact are not adequately prepared or designed. This emphasizes the importance of proper application techniques when leveraging thermal management materials.
Durability and Longevity Factors
Aside from thermal conductivity, the durability of thermal management materials is of equal importance. Factors such as compression set, tensile strength, and resistance to environmental conditions (temperature, humidity, and chemicals) significantly influence longevity. For example, in automotive applications, materials must endure high temperatures and vibrations without degradation.
High-quality thermal management materials often undergo rigorous testing to assess their lifespan under different conditions. Selecting materials with proven performance data can save businesses from costly failures and recalls, ensuring that devices operate efficiently over time.
Cost vs. Performance Analysis
When choosing thermal management materials, a careful evaluation of cost against performance is essential. While cheaper materials may appear cost-effective initially, they can lead to increased operational costs due to frequent replacements or repairs from overheating issues. Thus, investing in higher-quality materials can yield savings in the long run by enhancing reliability and reducing labor costs associated with maintenance.
Companies must also consider not just the price per unit but the overall performance potential of thermal management materials in the context of their specific applications. A thorough cost-benefit analysis helps in making informed decisions that align with project budgets while ensuring quality standards are met.
Applications of Thermal Management Materials
Electronics Cooling Solutions
The primary application of thermal management materials is in cooling solutions for electronic devices. From smartphones and laptops to servers and industrial machinery, managing heat is vital for device performance. Thermal interface materials, gap fillers, and thermal pads are commonly implemented in these scenarios.
For instance, in high-performance computing systems where CPUs generate significant heat, effective TIMs create a better thermal interface between the CPU and the heat sink, resulting in lower overall temperatures and increased reliability. Failure to utilize appropriate thermal management materials can lead to thermal throttling and device failures.
Automotive and Aerospace Uses
The automotive and aerospace industries present particularly challenging environments for thermal management materials. Both sectors require materials that can withstand fluctuating temperatures, mechanical vibrations, and exposure to chemicals. In automotive applications, for example, materials such as thermal pads and gap fillers are utilized around electronic control units (ECUs) and in battery management systems for electric vehicles.
Aerospace applications call for materials with excellent performance at extreme altitudes and temperatures. Specialized PCMs are integral in managing the thermal loads on electronic systems aboard aircraft and spacecraft, helping to ensure the stability of critical operations.
Consumer Electronics Considerations
In the realm of consumer electronics, the trend towards thinner devices has increased the importance of effective thermal management. Products such as smartwatches, tablets, and smartphones must maintain low operational temperatures despite their compact designs. Here, thermal interface materials and thermal pads play a crucial role.
With consumers holding manufacturers accountable for device performance and reliability, the integration of high-quality thermal management solutions has become indispensable. Companies investing in these materials are likely to gain a competitive edge by enhancing user satisfaction and reducing product failures.
Choosing the Right Thermal Management Materials for Your Needs
Assessment Criteria and Best Practices
Selecting the appropriate thermal management material involves a comprehensive assessment of the application requirements. Key criteria to consider include:
- Thermal Performance: Assess the thermal conductivity required for your specific application.
- Mechanical Properties: Consider the material’s ability to withstand mechanical stress, vibration, and compression.
- Environmental Stability: Determine the temperature ranges and environmental conditions that the material will encounter.
- Ease of Application: Evaluate how easily the material can be applied in a production environment.
- Cost Considerations: Weigh the cost against the expected performance and longevity.
Consulting with manufacturers or suppliers can provide further insights and assist in finding optimal solutions tailored to specific thermal management needs.
Customization Options and Solutions
Furthermore, many companies now offer customization options for thermal management materials to meet unique application demands. This could include bespoke formulations of thermal interface materials or specialized sizes and shapes of thermal pads and gap fillers.
Customization not only enhances performance but can also lead to efficiencies in the manufacturing process by reducing waste and streamlining assembly. Engaging with suppliers early in the product development cycle can yield innovative solutions that set a project apart from competitors.
Supplier Comparisons and Recommendations
With many suppliers available on the market, it is essential to compare options based on quality, performance data, and customer support. Leading manufacturers such as Henkel, DuPont, and Laird Technologies provide a range of thermal management solutions, each with distinct properties suited to various applications.
Additionally, reviewing case studies and product testimonials can provide valuable insights into supplier reliability and effectiveness. Building strong relationships with suppliers ensures ongoing support and can lead to significant benefits throughout a product’s lifecycle.
Future Trends in Thermal Management Materials
Innovations in Material Technologies
The landscape of thermal management materials is rapidly evolving. Innovations in material science are paving the way for the development of advanced thermal management solutions. Researchers are exploring new composites that combine the properties of different materials to improve thermal conductivity while maintaining mechanical strength.
Additionally, the integration of nanotechnology is proving promising in enhancing the performance of existing materials. Nanomaterials can significantly reduce thermal resistance and enhance performance, thus addressing the challenges posed by modern, high-density electronics.
Market Growth and Emerging Applications
The global thermal management market is poised for growth as the demand for efficient thermal solutions rises across various industries. Enhanced cooling requirements in sectors such as electric vehicles, renewable energy systems, and high-performance computing are creating new opportunities for thermal management materials.
Emerging technologies such as 5G and IoT devices also create fresh challenges, necessitating the continued evolution of thermal management strategies. Companies are encouraged to remain agile and adapt to these market changes, ensuring that they leverage the latest materials to stay ahead.
Environmental Considerations and Sustainability
As sustainability becomes a focal point for manufacturers and consumers alike, the development of eco-friendly thermal management materials is gaining traction. Innovations in biodegradable materials and the recycling of thermal interfaces are emerging trends that address environmental concerns without compromising performance.
Investing in sustainable thermal management solutions not only benefits the environment but can also enhance a brand’s image and appeal to eco-conscious consumers. Companies willing to lead in sustainability efforts may find themselves at a competitive advantage in the marketplace.